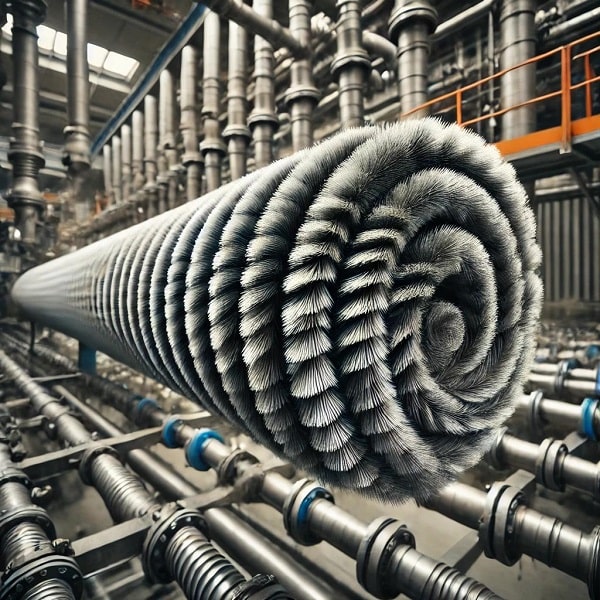
Les brosses cylindriques en spirale sont des outils industriels très utilisés dans diverses applications de nettoyage et de traitement de surfaces. Leur conception unique, avec des filaments en spirale autour d’un axe central, permet une efficacité maximale dans des environnements variés. Avec les avancées récentes, ces brosses ont été adaptées pour répondre à des besoins de plus en plus spécifiques. Voyons de plus près les innovations récentes dans ce domaine.
Qu’est-ce qu’une brosse cylindrique en spirale ?
Une brosse cylindrique en spirale est une brosse qui comporte des filaments disposés en spirale autour d’un noyau central. Elle peut être utilisée pour des tâches de nettoyage, de polissage ou de préparation de surfaces. En fonction de l’application, elle peut être fabriquée à partir de différents matériaux, tels que le nylon, le métal, ou des fibres synthétiques. Dans certaines applications, on utilise aussi la brosse disque pour des nettoyages spécifiques de surfaces planes ou courbes.
Applications traditionnelles
Avant de se concentrer sur les innovations récentes, il est important de comprendre les applications classiques des brosses cylindriques en spirale :
- Nettoyage de tubes et de conduits : Ces brosses sont souvent utilisées pour nettoyer l’intérieur des tuyaux et des canalisations. Leur forme cylindrique permet un contact optimal avec les parois, ce qui les rend très efficaces pour enlever la saleté, les graisses et les résidus.
- Polissage de surfaces : Elles sont également utilisées pour le polissage de différentes surfaces métalliques ou en plastique dans des environnements industriels, comme l’automobile ou l’aérospatiale.
- Préparation de surfaces : Dans l’industrie de la métallurgie, ces brosses sont utilisées pour désoxider ou dégraisser des pièces avant de les peindre ou de les traiter.
Innovations récentes
Avec les progrès technologiques, les brosses cylindriques en spirale ont évolué pour répondre à des besoins plus spécifiques. Voici quelques-unes des innovations récentes :
- Brosses avec des matériaux composites : Des brosses cylindriques en spirale sont maintenant fabriquées avec des matériaux composites avancés, combinant la légèreté des plastiques et la durabilité des métaux. Cela permet d’obtenir des performances de nettoyage optimales tout en réduisant l’usure des filaments et en augmentant leur durée de vie.
- Brosses à haute résistance thermique : Pour les applications nécessitant des conditions de température extrêmes, comme dans l’industrie automobile ou aérospatiale, de nouvelles brosses sont conçues pour résister à des températures élevées. Elles sont fabriquées avec des filaments spécialement traités pour supporter des températures qui peuvent dépasser 300°C.
- Brosses adaptées aux matériaux sensibles : Dans l’industrie électronique ou pour le nettoyage de pièces délicates, des brosses cylindriques en spirale sont désormais disponibles avec des poils ultra-doux, permettant de nettoyer sans endommager les surfaces sensibles, comme les écrans ou les composants en verre.
- Technologie antistatique : Certaines brosses cylindriques en spirale intègrent désormais une technologie antistatique. Cela les rend idéales pour les environnements sensibles, comme les salles blanches et les industries électroniques, où la moindre charge électrostatique pourrait endommager les équipements. Ces brosses dissipent l’électricité statique au fur et à mesure du nettoyage.
- Brosses modulaires et personnalisées : De plus en plus de fabricants proposent des brosses cylindriques modulaires qui peuvent être adaptées à des applications spécifiques. Les clients peuvent choisir la longueur, la rigidité des filaments et la forme des brosses en fonction de leurs besoins exacts.
En conclusion, les brosses cylindriques en spirale ont évolué avec les avancées technologiques pour répondre aux exigences spécifiques de divers secteurs industriels. Leur utilisation reste essentielle dans des domaines comme le nettoyage de surfaces, le polissage et la préparation de pièces, mais les innovations récentes, telles que l’utilisation de matériaux composites, la résistance thermique et les technologies antistatiques, les rendent encore plus adaptées aux applications modernes. Ces évolutions permettent non seulement d’améliorer la performance et la sécurité, mais aussi de prolonger la durée de vie des outils tout en répondant aux besoins particuliers de chaque industrie.